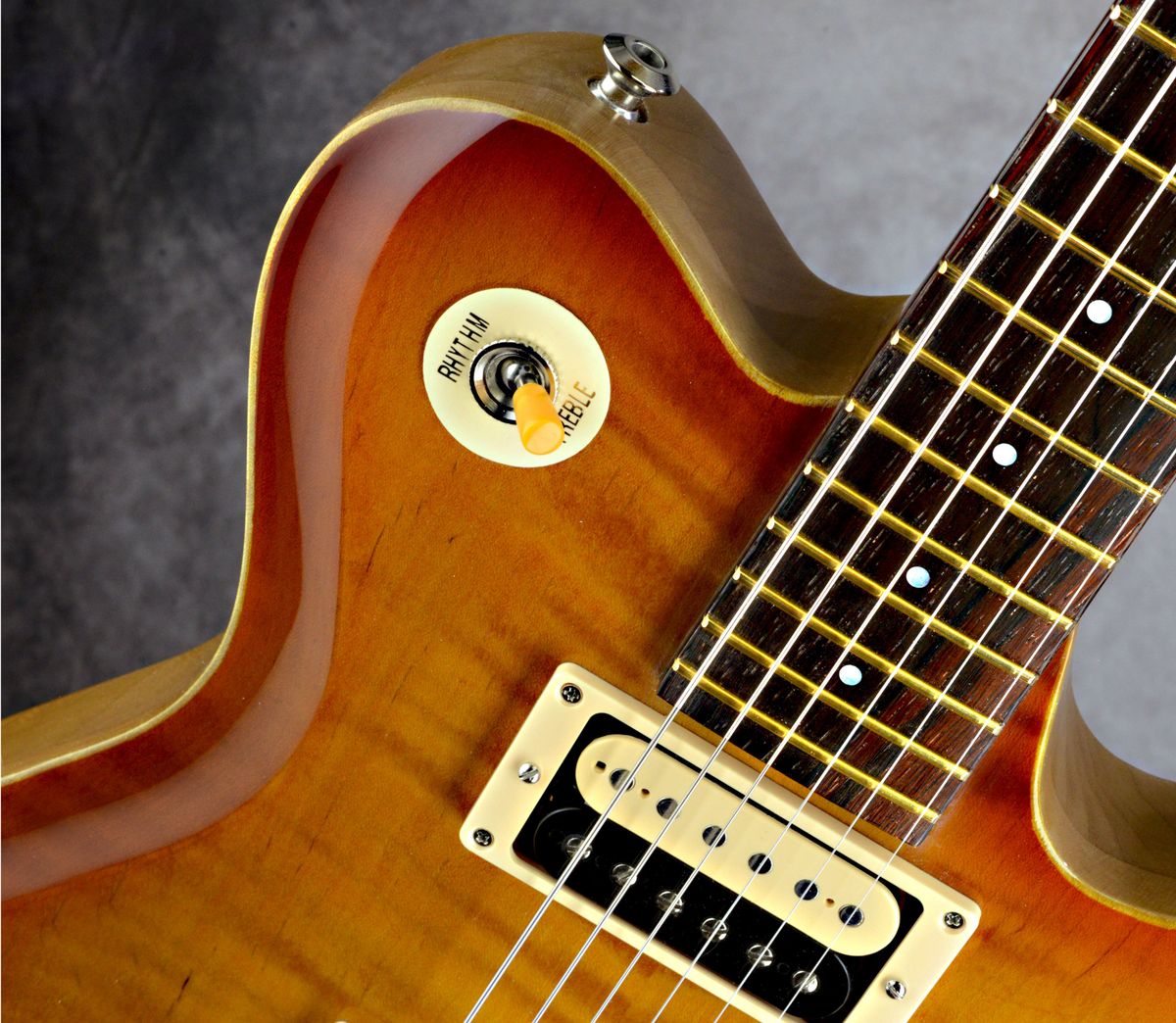
That’s a brand-new nitro lacquer burst finish on one of our columnist’s builds.
Nitro, poly, and more: what they’re made of, and why we love them.
In previous columns, I’ve touched on the subject of lacquer checking and the rise of relic finishes, but I thought a discussion of finishing materials might be in order as well. The terms nitro, poly, and lacquer, as well as other vague descriptions, are often used, and just as often, they’re misused and misunderstood. While I’m not a chemist and don’t pretend to know everything about coatings, I’ll try to outline some basic facts and how they relate to your guitar’s look, sound, and durability. But first, a little history.
Possibly the oldest decorative coatings are red and black lacquers from China that date back thousands of years. Chinese lacquer was primarily used to beautify luxury goods. Early lacquers were made from tree sap mixed with other organic ingredients for color and stability.
Shellac, made from the sticky secretions of the tiny lac insect, appeared in Asia and India around 1200 BCE. In the 17th century, shellac became popular in Europe among furniture and instrument makers. (Fun fact: It can take up to 90,000 insects to produce one pound of shellac.)
The word “lacquer” is a catch-all term for coatings made from resins, including tree pulp, sap, and chemically manufactured synthetics. These resins can be diluted with solvents, but not water. However, there is now a class of water-soluble finishes that are referred to as waterborne lacquer. Confusing, isn’t it?
For practical purposes, let’s divide coatings into two groups: thermoplastic, which cures by drying (solvent evaporation), and thermoset, which cures by a chemical reaction alone. All of these finishes are diluted with solvent in order to allow them to be sprayed or applied by a brush. A thermoplastic coating will release the carrier solvents over time, leaving the solid material behind. This can take from a few days to several weeks depending on the lacquer’s particular formulation and the temperature and humidity of the paint room.“While back in the day it was difficult for builders to find suitable coatings that didn’t check, today it’s hard to find a lacquer that will.”
Nitrocellulose lacquer is thermoplastic. Made from trees, it’s loved for its ease of use, warm feel, and attractive sheen. To visualize the finishing process, think of thermoplastic like mud. Dirt (solids) plus water (solvent) equals mud. It’s easy to smear it on a surface, and when the water evaporates, it’s a somewhat hard finish. If you put water on your dried surface, it becomes mud again. In a similar way, a thermoplastic finish never completely cures. Nitro lacquer is able to be repaired easily with more nitro. The solvents in the repair material soften the original finish and they “melt” together. This also makes these finishes susceptible to damage from certain aggressive solvent-based cleaners like alcohol or turpentine.
Thermoset finishes, like polyester and catalyzed polyurethane, are for the most part impervious to most solvents because they are chemically cured. Thermoset coatings are typically two- or three-part mixtures which, when combined before application, react chemically (catalyze) to harden. Once they “lock,” they are set indefinitely. Anyone who has mixed two-part epoxy will be familiar with this process. While more difficult to repair, damaged thermoset finishes can be fixed with proper surface prep. Although the edge of a spot repair on a thermoset finish can be hard to disguise, some modern cyanoacrylate (superglue) repairs can be practically invisible. The ability to mass-produce thermoset chemicals, and their fast curing cycle, has made it the leading type of finishing material for the auto industry starting in the 1950s, and the guitar industry in the 1970s.
Another appeal of thermosets from a manufacturing standpoint is resistance to chipping and cold checking. During the guitar boom of the 1960s, lacquer checking was such a concern that many factories moved to catalyzed thermoset finishes. These are sometimes called “polys,” but they actually encompass a wide variety of products including polyesters, catalyzed urethanes, and two-stage conversion varnishes. Although guitarists have recently embraced the beauty of this “defect,” most manufacturers of new instruments have switched to finishes in the thermoset family to avoid it. The downside is that some can feel sticky, especially on necks.
The truth of the matter is that today, even nitrocellulose lacquers are blended with enough additives that they can be hard to cold check. Which brings us to the relic aesthetic. While back in the day it was difficult for builders to find suitable coatings that didn’t check, today it’s hard to find a lacquer that will.
There’s really more to this story than space will allow. We haven’t touched upon acrylics, conversion varnishes, epoxies, and French polish variants, let alone the question of whether or not finishes affect sound. That’s for another day, but for now, you know that finish type makes a practical difference that you can see and feel.
- Bass Bench: The World of Finishes ›
- Acoustic Soundboard: Guitar Finishes and Care 101 ›
- DIY Relic’ing: Let’s Crack Some Lacquer ›
Tom Bedell in the Relic Music acoustic room, holding a custom Seed to Song Parlor with a stunning ocean sinker redwood top and milagro Brazilian rosewood back and sides.
As head of Breedlove and Bedell Guitars, he’s championed sustainability and environmental causes—and he wants to tell you about it.
As the owner of the Breedlove and Bedell guitar companies, Tom Bedell has been a passionate advocate for sustainable practices in acoustic guitar manufacturing. Listening to him talk, it’s clear that the preservation of the Earth’s forests are just as important to Bedell as the sound of his guitars. You’ll know just how big of a statement that is if you’ve ever had the opportunity to spend time with one of his excellently crafted high-end acoustics, which are among the finest you’ll find. Over the course of his career, Bedell has championed the use of alternative tonewoods and traveled the world to get a firsthand look at his wood sources and their harvesting practices. When you buy a Bedell, you can rest assured that no clear-cut woods were used.
A born storyteller, Bedell doesn’t keep his passion to himself. On Friday, May 12, at New Jersey boutique guitar outpost Relic Music, Bedell shared some of the stories he’s collected during his life and travels as part of a three-city clinic trip. At Relic—and stops at Crossroads Guitar and Art in Gilbertsville, Pennsylvania, and Chuck Levin’s Washington Music Center in Wheaton, Maryland—he discussed his guitars and what makes them so special, why sustainability is such an important cause, and how he’s putting it into practice.
Before his talk, we sat in Relic’s cozy, plush acoustic room, surrounded by a host of high-end instruments. We took a look at a few of the store’s house-spec’d Bedell parlors while we chatted.
“The story of this guitar is the story of the world,” Bedell explained to me, holding a Seed to Song Parlor. He painted a picture of a milagro tree growing on a hillside in northeastern Brazil some 500 years ago, deprived of water and growing in stressful conditions during its early life. That tree was eventually harvested, and in the 1950s, it was shipped to Spain by a company that specialized in church ornaments. They recognized this unique specimen and set it aside until it was imported to the U.S. and reached Oregon. Now, it makes the back and sides of this unique guitar.
A Bedell Fireside Parlor with a buckskin redwood top and cocobolo back and sides.
As for the ocean sinker redwood top, “I’m gonna make up the story,” Bedell said, as he approximated the life cycle of the tree, which floated in the ocean, soaking up minerals for years and years, and washed ashore on northern Oregon’s Manzanita Beach. The two woods were paired and built into a small run of exquisitely outfitted guitars using the Bedell/Breedlove Sound Optimization process—in which the building team fine-tunes each instrument’s voice by hand-shaping individual braces to target resonant frequencies using acoustic analysis—and Bedell and his team fell in love.
Playing it while we spoke, I was smitten by this guitar’s warm, responsive tone and even articulation and attack across the fretboard; it strikes a perfect tonal balance between a tight low-end and bright top, with a wide dynamic range that made it sympathetic to anything I offered. And as I swapped guitars, whether picking up a Fireside Parlor with a buckskin redwood top and cocobolo back and sides or one with an Adirondack spruce top and Brazilian rosewood back and sides, the character and the elements of each instrument changed, but that perfect balance remained. Each of these acoustics—and of any Bedell I’ve had the pleasure to play—delivers their own experiential thumbprint.
Rosette and inlay detail on an Adirondack spruce top.
Ultimately, that’s what brought Bedell out to the East Coast on this short tour. “We have a totally different philosophy about how we approach guitar-building,” Bedell effused. “There are a lot of individuals who build maybe 12 guitars a year, who do some of the things that we do, but there’s nobody on a production level.” And he wants to spread that gospel.
“We want to reach people who really want something special,” he continued, pointing out that for the Bedell line, the company specifically wants to work with shops like Relic and the other stores he’s visited, “who have a clientele that says I want the best guitar I can possibly have, and they carry enough variety that we can give them that.”
A Fireside Parlor with a Western red cedar top and Brazilian rosewood back and sides.
ENGL, renowned for its high-performance amplifiers, proudly introduces the EP635 Fireball IR Pedal, a revolutionary 2-channel preamp pedal designed to deliver the legendary Fireball tone in a compact and feature-rich format.
The EP635 Fireball IR Pedal brings the raw power and precision of the ENGL Fireball amplifier into a pedalboard-friendly enclosure, offering unmatched flexibility and tonal control for guitarists of all styles. This cutting-edge pedal is equipped with advanced features, making it a must-have for players seeking high-gain perfection with modern digital convenience.
Key Features:
- Authentic Fireball Tone – Designed after the renowned ENGL Fireball amplifier, the EP635 delivers the unmistakable high-gain aggression and clarity that ENGL fans love.
- Two Independent Channels – Easily switch between two distinct channels, with each channel’s knob settings saved independently, allowing for seamless transitions between tones.
- Built-in Midboost Function – Enhance your tone with the integrated Midboost switch, perfect for cutting through the mix with extra punch.
- Advanced Noise Gate – Eliminate unwanted noise and maintain articulate clarity, even with high-gain settings.
- IR (Impulse Response) Loading via USB-C – Customize your sound with user-loadable IRs using the included software, bringing studio-quality cab simulations to your pedalboard.
- Headphone Output – Silent practice has never been easier, with a dedicated headphone output for direct monitoring.
- Premium Build and Intuitive Controls – Featuring a rugged chassis and responsive controls for Volume, Gain, Bass, Middle, Treble, and Presence, ensuring precise tonal shaping.
SPECS:
- Input 1/4” (6,35mm) Jack
- Output 1/4” (6,35mm) Jack
- Headphone Output 1/8”(3,5mm) Jack
- 9V DC / 300mA (center negativ) / power supply, sold separately
- USB C
The Gibson EH-185, introduced in 1939, was one of the company’s first electric guitars.
Before the Les Pauls and SGs, this aluminum-reinforced instrument was one of the famous brand’s first electric guitars.
It’s hard to overstate the importance of electric guitar in shaping American popular music over the last half-century. Its introduction was a revolution, changing the course of modern musical styles. Today, when we think of the guitars that started the revolution, we think of the Stratocaster and the Les Paul, guitars held against the body and fretted with the fingertips. But the real spark of this musical mutiny was the lap-steel guitar.
In the early 20th century, guitar music was moving out of the parlors of homes and into public spaces where folks could gather together and dance. Guitarists needed to project their sound far beyond where their wimpy little acoustic instruments could reach. Instrument manufacturers began experimenting with larger body sizes, metal construction, and resonators to increase volume.
Around this time, George Beauchamp began experimenting with electric guitar amplification. He settled on a design using two U-shaped magnets and a single coil of wire. Beauchamp was in business with Adolph Rickenbacker, and they decided to stick this new invention into a lap steel.
If we put on our 1930s glasses, this decision makes perfect sense. The most popular music at the time was a blend of Hawaiian and jazz styles made famous by virtuosos like Solomon “Sol” Hoʻopiʻi. Photos of Hoʻopiʻi with a metal-body resonator abound—one can imagine his relief at being handed an instrument that projected sound toward the audience via an amplifier, rather than back at his own head via resonator cones. Beauchamp and Rickenbacker were simply following the market.
As it turned out, the popularity of Hawaiian music gave way to swing, and electric lap steels didn’t exactly take the world by storm. But Beauchamp and Rickenbacker had proven the viability of this new technology, and other manufacturers followed suit. In 1937, Gibson created a pickup with magnets under the strings, rather than above like Beauchamp’s.
“When I plugged in the EH-185 I expected to hear something reminiscent of Charlie Christian’s smooth, clean tone. But what I got was meatier—closer to what I associate with P-90s: warm and midrange-y.”
The first page of Gibson’s “Electrical Instruments” section in the 1939 catalog features a glowing, full-page write-up of their top-of-the-line lap steel: the EH-185. “Everything about this new electric Hawaiian Guitar smacks of good showmanship,” effuses the copy. “It has smoothness, great sustaining power, and an easy flow of tone that builds up strongly and does not die out.”
Picking up the 1940 EH-185 at Fanny’s House of Music is about as close as one can get to traveling back in time to try a new one. It is just so clean, with barely any dings or even finish checking. Overall, this is a 9/10 piece, and it’s a joy to behold. Speaking of picking it up, the first thing you notice when you lift the EH-185 out of the case is its weight. This is a much heavier instrument than other similar-sized lap steels, owing to a length of thick metal between the body and the fretboard. The catalog calls it “Hyblum metal,” which may be a flowery trade name for an early aluminum alloy.
This 1940 EH-185 is heavier than other lap steels in its class, thanks to a length of metal between its fretboard and body.
Photo by Madison Thorn
There are numerous other fancy appointments on the EH-185 that Gibson didn’t offer on their lesser models. It’s made of highly figured maple, with diamond-shaped decorations on the back of the body and neck. The double binding is nearly a centimeter thick and gives the instrument a luxurious, expensive look.
Behind all these high-end attributes is a great-sounding guitar, thanks to that old pickup. It’s got three blades protruding through the bobbin for the unwound strings and one longer blade for the wound strings. When I plugged in the EH-185 I expected to hear something reminiscent of Charlie Christian’s smooth, clean tone. But what I got was meatier—closer to what I associate with P-90s: warm and midrange-y. It was just crying out for a little crunch and a bluesy touch. It’s kind of cool how such a pristine, high-end vintage instrument can be so well-suited for a sound that’s rough around the edges.
As far as electric guitars go, it doesn’t get much more vintage than this 1940 Gibson EH-185 Lap Steel. It reminds us of where the story of the electric guitar truly began. This EH-185 isn’t just a relic—it’s a testament to when the future of music was unfolding in real time. Plug it in, and you become part of the revolution.
Sources: Smithsonian, Vintage Guitar, Mozart Project, Gibson Pre-War, WIRED, Steel Guitar Forum, Vintaxe
J Mascis is well known for his legendary feats of volume.
J Mascis is well known for his legendary feats of volume. Just check out a photo of his rig to see an intimidating wall of amps pointed directly at the Dinosaur Jr. leader’s head. And though his loudness permeates all that he does and has helped cement his reputation, there’s a lot more to his playing.
On this episode of 100 Guitarists, we’re looking at each phase of the trio’s long career. How many pedals does J use to get his sound? What’s his best documented use of a flanger? How does his version of “Maggot Brain” (recorded with bassist Mike Watt) compare to Eddie Hazel’s? And were you as surprised as we were when Fender released a J Mascis signature Tele?