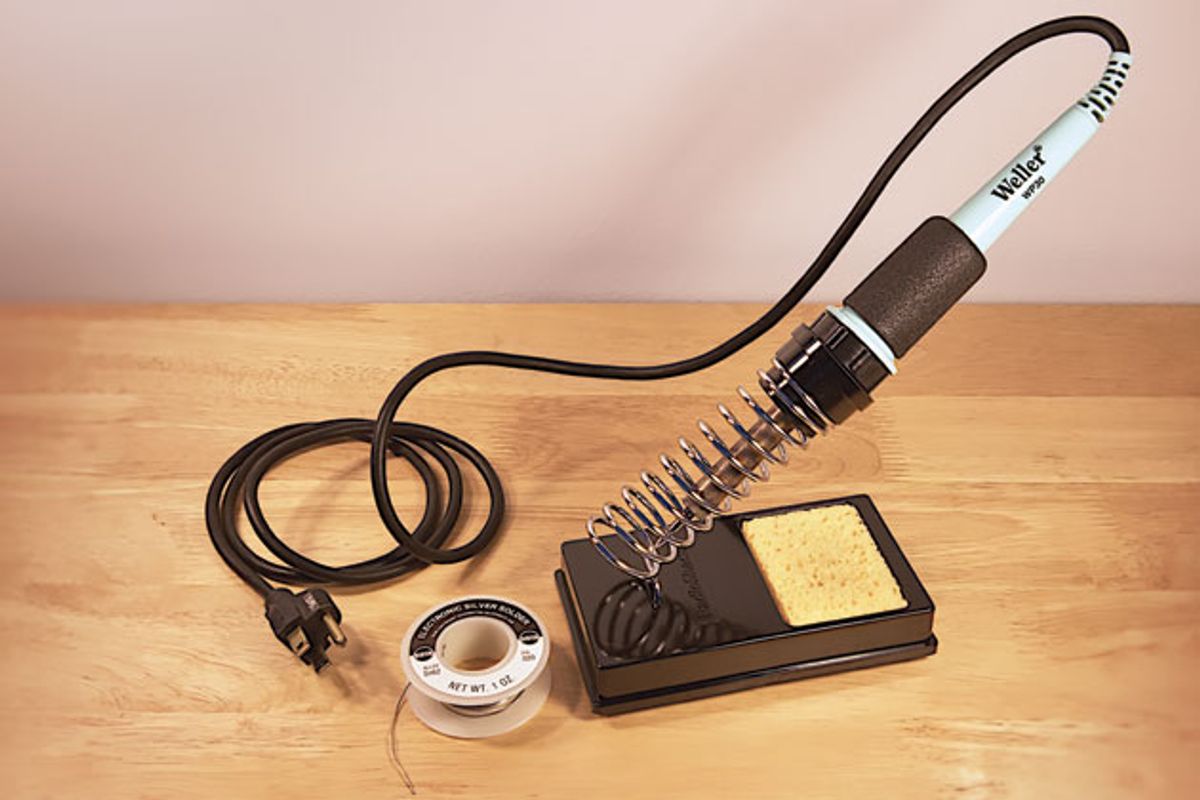
Photo 1 — The essentials: a low-watt soldering iron, a stand, a small damp sponge, and a roll of “electronic silver solder” like this .020" 60/40 tin/lead rosin flux solder from Kester.
Learn to solder like a pro in this easy-to-follow demonstration.
Given the DIY nature of this issue, we thought it would be appropriate to address good soldering technique. If you’re willing to invest a few bucks in some modest tools and spend a little time practicing the basics, you can learn to wire up guitars, stomp kits, speaker cabinets, and even do some simple amp mods. Once you understand the fundamentals, you can save money and derive a lot of satisfaction from working on your own gear.
The tools.
You’ll want a decent soldering pencil (a small type of soldering iron) rated at least 25 watts, but no more than 60 watts. (Many guitar techs like a 30-watt soldering iron for working on guitars and amps, and a 15-watt iron for working inside stompboxes and on delicate printed circuit boards.) You’ll also want a stand to hold the hot iron when not in use, a damp sponge, and some rosin core solder made for electronic work (Photo 1).
Photo 2 — If your soldering stand doesn’t house a sponge, just put a damp household sponge in a glass or ceramic dish. Other helpful tools: a hemostat and small clamps to hold parts still as you solder them, and a “solder sucker” bulb for removing solder.
You should also have some basic hand tools, such as wire strippers, needle-nose pliers, wire cutters, and something to hold the wire in place while a solder joint cools (Photos 2 and 3).
Photo 3 — In addition to hook-up wire, you’ll want wire strippers. Alternatively, luthier suppliers offer old-school “push-back” wire with a waxed cotton jacket (center) that eliminates the need for stripping off the plastic insulation from the end of the wire. Electrical tape and heat shrink tubing come in handy when you need to protect or insulate your work.
There are tools sold specifically for holding wires and parts, available through an electronics supply house.
Step 1: Prepare the Joint
Photo 4 — Before you attempt to solder a connection, the wire and component must be secured to assure they remain absolutely motionless. Here, a spring-loaded heat-sink clamp holds the wire in place while a vice grip gently clamps the pot shaft.
For every joint, you need to find a way to hold the wire in position without using your hands (Photo 4). Wrap the wire through the solder lug once to make it hold tightly on its own, use tape to hold it in place, lay a pair of pliers on the wire to hold it firmly where you want it, or use a mechanical soldering aid to hold it. Use whatever works, except holding the wire manually. When you make a solder connection and rely on your hands to hold the soldered wire steady while the joint cools, you will fail—no human hands are steady enough to hold anything perfectly still, and you want the wire to remain absolutely motionless while it cools. If there is movement, the result will be internal fractures in the solder.
Step 2: Clean the Tip
Photo 5 — Wipe the hot tip with a damp sponge to keep it clean.
The tip must be cleaned before each and every joint—you can use the damp sponge for this (Photos 5 and 6).
Photo 6 — A clean, dross-free tip looks smooth and shiny.
Solder produces a by-product called dross very, very quickly, and the dross fouls the tip, preventing good heat conduction and introducing waste material into your solder joints.
Step 3: Tin the Tip
Photo 7 — Add a small amount of solder to a freshly cleaned tip just before you solder a connection. When you see this telltale puff of smoke, pull the strand of solder off the tip, shake off any excess, and then move quickly to the joint.
Immediately before you get on the joint with the heat, add fresh solder to the tip of the iron to “tin” it. Simply feed solder directly onto the tip so it’s completely coated (Photo 7). A tinned tip will provide much better heat conduction than a tip that’s clean but not tinned.
Step 4: Remove the Excess Solder
Shake off the excess solder after tinning—you want the tip coated, but not dripping. I have a fire-resistant container beside my soldering bench, and after tinning I tap the barrel of my iron on the edge of the container to knock excess molten solder into it. You can use any fire-resistant container for this, such as a tin can or ceramic bowl, but use care not to start a fire. Because solder melts at such a low temperature the risk of a fire is very low—molten solder is unlikely to ignite even highly flammable materials like paper—but use care anyway!
Step 5: Get on the Joint Right Away
As soon as you’ve removed the excess solder from the tip, get right on the joint. By “joint,” I mean the wire and the solder lug, or the wire and the back of the pot, or whatever it is you’re soldering. Dross will start to form on the tip very quickly, so as soon as the tip is prepared, get to work.
Step 6: Heat the Joint
Photo 8 — Gently press the iron’s hot tip against the joint to heat it before you bring the solder into the equation. The goal is to make the joint itself hot enough to melt the solder.
Heat the joint, not the solder (Photo 8). You want the joint to be hot enough to melt the solder. It’s a given that the iron is hot enough to melt it—just feed a little onto the tip and you’ll see—but you also want the joint itself to be hot enough to do the same.
Photo 9 — While holding the tip against the joint, feed the solder onto the heated joint, not the soldering iron tip. Here the emerging puff of smoke indicates the solder is melting.
If you feed solder onto the joint without it touching the iron (Photo 9), the solder will melt and be attracted right to the joint. You can watch the solder actually wick out onto the surface you’re soldering to—this is what you want.
Step 7: Get off the Joint
As soon as the solder has flowed onto the joint properly, remove the heat from the joint. Most components can stand a fair amount of heat, but some are more susceptible to damage than others, so there’s no need to push your luck. Pots are fairly durable (unless it’s a cheap pot), so it’s highly unlikely you’ll damage one by trying to solder a wire to its back. But again, there’s no need to push your luck, so as soon as you’ve completed the joint, pull the iron away and let the joint cool with the components remaining motionless.
Photo 10 — When the molten solder has flowed into the joint, pull away both the solder and iron. Keep the joint motionless as it cools and don’t blow on it—the moisture in your breath will enter the cooling connection and potentially cause it to fail.
If you’re soldering to a ring-shaped solder lug, then you’ll want to fill it completely with solder (Photo 10). This will maximize the mechanical strength of the joint.
Like most skills, soldering proficiency is acquired through practice. Employing good technique will allow you to become competent all the more quickly, so follow these steps, and you’ll be soldering like a pro in no time. You should probably practice on projects that aren’t expensive or mission critical—you might want to think twice about rewiring your only guitar before that gig with Clapton tonight. But if you keep at it, you’ll be one step closer to being a consummate DIY’er.
Two Ways to Improve Your Soldering Projects
After you master the basics, there are two more skills to add to your bag of tricks: removing old solder and installing heat shrink tubing. There are plenty of occasions where you’ll wish you could remove old solder and re-use a part. For example, you might have rescued a volume or tone pot from a previous mod or project. If it’s a high-quality pot, like those from CTS, why toss it and buy a new replacement when you can put the old one back into service? It’s easy to reverse the soldering process and remove old solder and bits of wire. You simply need a solder removal tool. There are several types, including disposable braided wire that’s designed to wick molten solder away from a joint, and various vacuum pump tools and “solder suckers.” I prefer a simple rubber bulb with a heat-resistant Teflon tip.
Photo 11
Here’s how it works: Stabilize your component, in this case, a pot (Photo 11). See how one lug is filled with solder? Let’s make that go bye-bye. Apply heat to the lug with a freshly cleaned soldering-iron tip.
Photo 12
When you see the solder turn shiny and molten, hold the bulb away from the lug, squeeze and hold the bulb, and then bring its tip to the lug and release the bulb. Fffffft! The molten solder goes up the tip and into the bulb (Photo 12).
Photo 13
Look at that—a nice clean lug ready for its next mission (Photo 13).
Tip:It’s good to recycle pots and parts, but never try to reuse old solder. Clean it off and start fresh.
In case you’re wondering what happens to the old solder, every few months you simply work the tip out of the bulb, shake the collected cold solder beads into the trash, and reinsert the tip into the bulb. Good to go.
When you’re working with wire and electronics, you’ll often encounter instances where you need to insulate a connection from other wires or components. For example, you want to install a favorite old pickup into another guitar. However, the pickup leads have been cut back over the years and now they won’t reach the intended switch or pot, which means it’s time to splice short extensions to the pickup leads. No problem, except if the exposed wires touch each other or other components, they’ll create a short and you’ll hear only silence (or an annoying hum).
Electrical tape will do the job to insulate the splices, but heat shrink tubing—aka heat shrink—offers a more elegant solution. To make this work, you’ll need a heat source. Some folks use a lighter, but I prefer a heat gun because I like to avoid open flame in my workshop. Heat guns aren’t expensive and they get the job done efficiently and safely.
Photo 14
The details: Designed to slide over wire of different gauges, heat shrink comes in various diameters. After you select the right diameter to comfortably slip over your wire, cut off a piece that will straddle the solder splice or joint you plan to cover. The pros suggest a length that’s about three times as long as the exposed section. Use hemostats or a clamp to temporarily hold the ends together while you gauge the length you’ll need to cut (Photo 14).
Photo 15
Next, remove the clamp, slide the heat shrink over one end of the wire (keep it far away from your hot iron) and solder the wires. When the solder has cooled, slip the heat shrink over the new joint, center it, and fire up the heat gun. The tubing will start to immediately contract around the joint (Photo 15). Don’t worry, air from the heat gun doesn’t get hot enough to compromise the solder joint. Once the tubing has completely closed up around the wire, you’re done. The joint now has a tough, new skin to protect it. —Andy Ellis
[Updated 1/13/22]
- Three Must-Try Guitar Wiring Mods - Premier Guitar ›
- The ABCs of Output Jacks - Premier Guitar ›
- The Stompbox-Builder's Secret Weapon - Premier Guitar ›
Brent Mason is, of course, on of the most recorded guitarists in history, who helped define the sound of most ’90s country superstars. So, whether you know it or not, you’ve likely heard Mason’s playing.
Professional transcriber Levi Clay has done the deepest of dives into Brent Mason’s hotshot licks. At one point, he undertook the massive project of transcribing and sharing one of Mason’s solos every day for 85 or so days. Mason is, of course, on of the most recorded guitarists in history, who helped define the sound of most ’90s country superstars. So, whether you know it or not, you’ve likely heard Mason’s playing. Levi shares the insight he gleaned from digging deep, and he tells us what it was like when they shared a stage last year. Plus, Levi plays us some great examples of Mason’s playing.
For the first time ever, two guitar greats, John 5 and Richie Kotzen will be heading out on the road this year. The tour will launch October 16 and run through November, hitting markets across the U.S.
Find the full tour itinerary right plus a link for tickets & VIP, including additional dates featuring John 5 only. Reserved seating tickets will go on sale Friday May 16 though a fan presale will begin today at noon local time and fans are strongly encouraged to buy early to get the best seats.
Meet and Greets for both artists will be available. For John 5 please go to: https://john5store.com/collections/vip.
Today, John 5 also announces more details of his anticipated new album. Called The Ghost, it will be released October 10 and is led by the new track “Fiend,” featuring Kenny Aronoff.
John 5 continues running public tours this month for his Knights In Satan’s Service Museum of KISS Memorabilia in Los Angeles, California. Guided tours are open to the public for one month only (with a possible expansion). Current dates available are May 12-16, May 19-23 and May 27-30. Each will be led by John 5 himself who will provide tons of rich detail and answer any questions. Secure your place HERE.
JOHN 5 continues to tour with Mötley Crüe including an upcoming residency in Las Vegas in 2025.RICHIE KOTZEN &
JOHN 5 FALL 2025 TOUR
October 16 El Cajon, CA @ Magnolia
October 17 Riverside, CA @ Fox Performing Arts
October 18 Roseville, CA @ Goldfield Trading Post
October 19 San Jose, CA @ The Ritz
October 21 Phoenix, AZ @ Celebrity Theatre
October 22 Albuquerque, NM @ KiMo Theatre
October 24 Dallas, TX @ Granada Theater
October 25 Leander, TX @ The Haute Spot
October 27 New Orleans, LA @ House of Blues
October 28 Memphis, TN @ Minglewood Hall
October 29 Nashville, TN @ Fogg Street Lawn Club
October 30 Atlanta, GA @ Variety Playhouse
October 31 Orlando, FL @ House of Blues
November 1 Fort Lauderdale, FL @ Culture Room
November 2 Clearwater, FL @ Capitol Theatre
November 4 Richmond, VA @ The National
November 5 Leesburg, VA @ Tally Ho Theater
November 6 Patchogue, NY @ Patchogue Theatre
November 11 Glenside, PA @ Keswick Theatre
November 12 Derry, NH @ Tupelo Music Hall
November 13 Foxborough, MA @ Six String Grill & Stage
November 14 Stroudsburg, PA @ Sherman Theater
November 15 Lorain, OH @ Lorain Palace Theatre
November 16 Columbus, OH @ The King Of Clubs
November 17 Warrendale, PA @ Jergels
November 19 Wyandotte, MI @ District 142
November 20 Flint, MI @ The Machine Shop
November 21 Fort Wayne, IN @ Piere’s
November 22 St. Charles, IL @ Arcada Theatre
November 23 Belvidere, IL @ Apollo Theatre
November 25 Denver, CO @ Oriental Theater
November 29 Pioneertown, CA @ Pappy & Harriet's*
*John 5 only
AEROSMITH guitarist and songwriter JOE PERRY is set to return to the road for a series of August performances with THE JOE PERRY PROJECT. The 8-date run kicks off August 13 in Tampa, FL and wraps August 23 in Port Chester, New York, with an August 19 performance in PERRY’s Boston hometown (see the itinerary below). For the North American trek—which marks the first solo shows for PERRY this year—the legendary guitarist will be joined by his Aerosmith bandmates Brad Whitford (guitar) and Buck Johnson (keys), along with The Black Crowes’ Chris Robinson (vocals), and Stone Temple Pilots’ Robert DeLeo (bass), and Eric Kretz (drums).
“Well…it’s time to let the music do the talkin again,” PERRY says. “I’m really excited about the JPP line up this year!!!! Most of these guys played with me at The Roxy in L.A. at the debut event for my latest solo album [Sweetzerland Manifesto] in January 2018. They’re all busy as hell but thankfully they’re able to carve out some time for this run. And I’m not only lucky enough to have Brad Whitford onstage with me but Chris Robinson of The Black Crowes! [who sang ‘Fortunate One’ on Sweetzerland Manifesto MKII], Robert DeLeo and Eric Kretz from STP!!! and Buck Johnson who plays keys and sings with Aerosmith, the Hollywood Vampires, and is also a solo artist in his own right.”
For the shows, the Rock and Roll Hall of Fame inductee says “the set list is gonna include my fav JPP cuts, STP, Black Crowes, and with Brad we’ll be hitting the Aero hits and some deep cuts and then ya never know!!!! Gonna be a BLAST, and if you’ve ever been to one of my shows you know the words GARAGE BAND on STEROIDS come to mind! See you there!!!!”
DATE | LOCATION | VENUE |
Wednesday, August 13 | Tampa, FL | Seminole Hard Rock - Tampa |
Thursday, August 14 | Hollywood, FL | Seminole Hard Rock - Hollywood |
Saturday, August 16 | Toronto, ON | HISTORY |
Sunday, August 17 | Muskoka, ON | Kee to Bala |
Tuesday, August 19 | Boston, MA | Wang Theatre |
Wednesday, August 20 | Hampton Beach, NH | Hampton Beach Casino Ballroom |
Friday, August 22 | Mashantucket, CT | The Premier Theater at Foxwoods Resort Casino |
Saturday, August 23 | Port Chester, NY | Capitol Theatre |
A sample page from the author’s analog log.
Seasonal changes are tough on your acoustic. Here’s how you can take better care of your prized instrument.
As you read this, spring is in bloom in most of the US, or maybe it has been for some time. I’m timing this column specifically to ask acoustic guitarists, in this season of increasing humidity and comfortable conditions, to prepare for what’s coming. It’s never too soon, and time flies. Before you know it, we’ll be back to the maintenance phase and you might be blowing up the phones of your local guitar shops, luthiers, and techs. I’m here to encourage a decidedly old-school approach to preventative guitar maintenance, and yes, it starts now.
Why, you ask? Well, as the lead luthier at Acoustic Music Works, I can tell you that in my nearly 15 years in this position, this was the worst winter ever for preventable repairs on acoustic guitars. Fret sprout, bridge lifts, top sink, soundboard cracks, back cracks, loose binding, general malaise… These hit us very hard in the winter that spanned 2024 and 2025. Am I complaining? On the one hand, no. This is part of how we make our money. On the other hand, yes! Repair schedules related to dryness and humidity issues can stretch into weeks and even months, and nobody wants to be without their favorite instruments for that amount of time. With a little thoughtfulness, however, you might get through next winter (and every one thereafter) without hefty repair bills or time apart from your musical companion.
Our preparation is going to start with an unlikely but very important guitar accessory: the humble notebook. Plain, lined, grid, day planner… it doesn’t matter. We all need to actively participate in our instrument maintenance, and in my experience, fancy apps that track humidity via Bluetooth breed a kind of laziness, a feeling of safety that might prevent us from actually physically looking in on conditions. Better we keep an analog, well, log, so that we know where things stand, and I suggest checking in daily.
“This was the worst winter ever for preventable repairs on acoustic guitars.”
Track your relative humidity, both in the case and in the room where your instruments mostly reside, but also take notes on your action height, top deflection (StewMac has some great tips for measuring this) and anything related to playability that you believe you can observe empirically.
Dryness is the root cause of most guitar issues that manifest in the fall and winter months. Symptoms of dryness include sharp fret ends, falling action and dead frets, sunken top around the sound hole, and cracks and bridge lifts. With your trusty notebook, you’ll get a feel for the sensitivity level of your instrument, and that knowledge is power!
A few other basic implements will not only assist you in your observations, but may also satisfy your need to buy guitar-related things (at least for a minute). Getting quick and comfortable with a fret rocker is a great skill to have, and is invaluable in diagnosing buzzes due to high frets or frets that have come unseated due to dryness. A well-calibrated relief gauge might seem luxurious, but it can prevent you from making unnecessary or extreme truss rod adjustments. A string action gauge, or even a simple machinist’s rule or set of feeler gauges, will help you keep track of your action. Get a three-pack of hygrometers so you can average their readings, rather than depending on one.
Lest we forget: A guitar can not only be too dry, it can also be too wet. By beginning your maintenance diligence in the spring/summer, you’ll also be able to tell if your instrument is the victim of a too-humid environment. The signs of over-humidification are subtle: Your action may rise from a puffed-up top, and in extreme cases, glue joints could begin to fail. In my experience, an over-humidified guitar will suffer from dulled tone, almost like a sock in the sound hole. If you’re sensing a lack of clarity in your guitar all of a sudden, start with new strings. If it persists, it might be due to over-humidification, and you may want to introduce a desiccant to the case for a time. The more lightly built your guitar is, the more sensitive it will be to seasonal changes.
By getting into these habits early, you’ll be empowered by knowing your instrument more intimately. You’ll understand when and why changes in tone and playability might have occurred, and you’ll hopefully save on repair bills year-round. Feel free to reach out with any questions. Who knows? I might just send you a notebook with an AMW sticker on the cover!