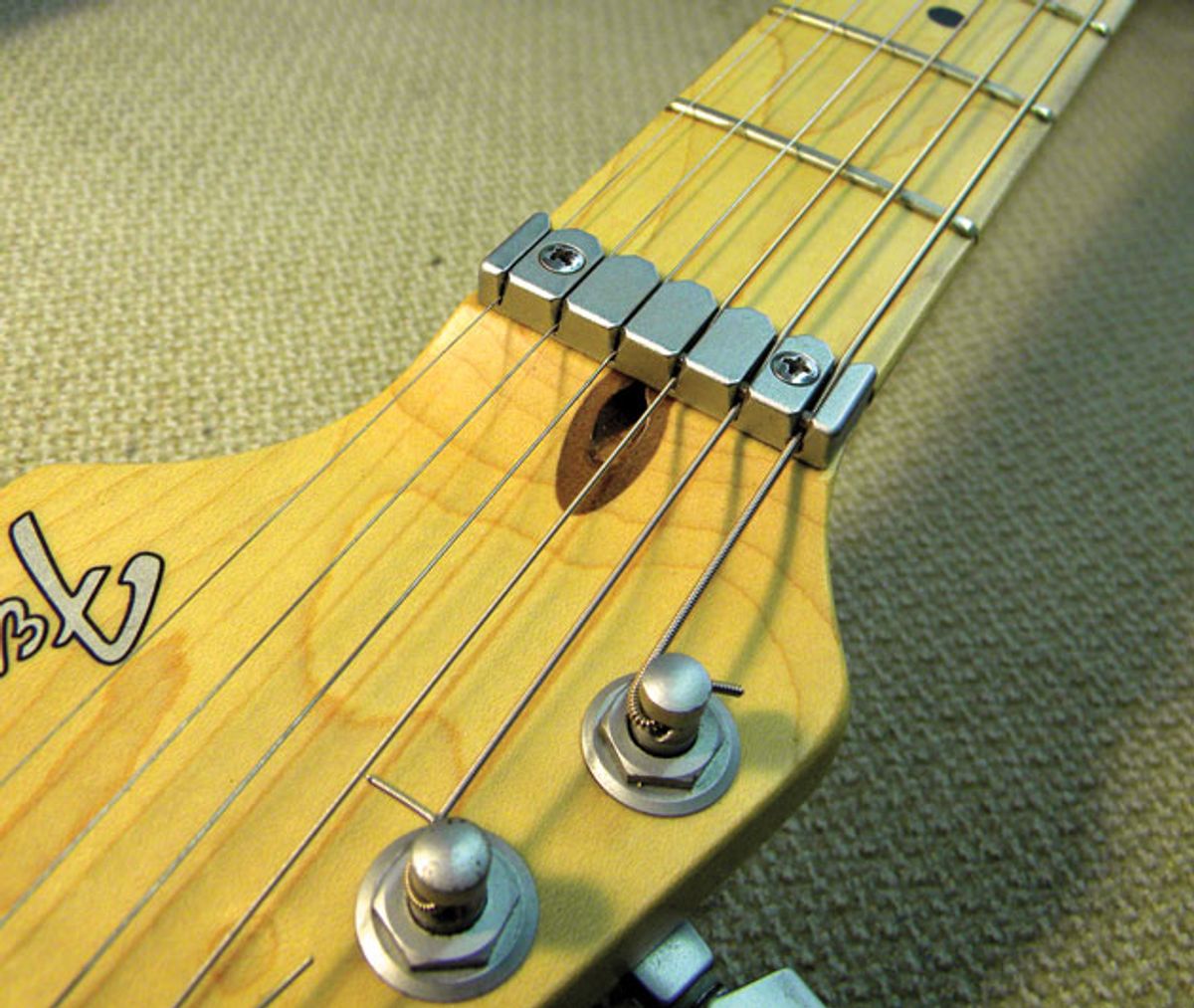
Replacing a stripped truss-rod nut can be an inexpensive DIY repair—if you know how to approach it.
Recently a client brought a fairly new American Fender Strat into the shop. The neck had too much relief, but otherwise the guitar was in great shape. No problem, I thought. Tighten up the truss rod a bit and we’ll be good to go.
I unwrapped a new Fender hex key (more about the condition of your tools in a moment) and inserted it into the truss rod nut. But instead of finding a secure grip, I felt the tool spin around inside the nut. Oh, that sinking feeling: I realized the nut’s socket was stripped, which is very bad news for this particular Strat.
Why? The truss rod nut on this type of Strat is recessed into the neck and surrounded by wood (Photo 1), so when the socket that holds the truss rod tool is stripped out, you only have two options: perform major surgery to remove the stripped nut and replace it with a new one, or buy a replacement neck. Realistically, it would cost more to perform the extraction, so I advised my client to contact Fender about getting a new neck.
Fortunately, not all Fender guitars have a recessed truss rod nut—in fact, many guitars don’t. You can often replace a stripped truss rod nut, and it’s not a tricky repair if you know what you’re doing. Inexpensive replacement nuts are available from such suppliers as Stewart-MacDonald, Luthiers Mercantile, and Allparts.
Different types of truss rod nuts.
Before we discuss why a truss rod nut might fail and how to fix it, let’s explore several common types of nuts used on guitars. You adjust some nuts by inserting a tool into them, others by enclosing them with a nut driver or special socket wrench.
Using the wrong tool to adjust a nut is the most common cause of truss rod problems.
The nut placement varies too: On Taylor and Gibson instruments, for example, the truss rod nut is typically located at the headstock, under a plastic or wood cover. These are among the easiest to remove. Some Fender guitars have a “bullet” truss rod nut at the headstock; these are not recessed and can be removed without surgery. Older Fender guitars have a truss rod nut at the heel of the fretboard, and these are very easy to remove, once you take off the neck. Some modern electrics have an exposed “wheel” nut located at the heel, and these can be adjusted without removing the neck.
Some acoustics, such as Takamine and modern Martins, have a truss rod nut that you access through the soundhole by inserting the tool through a small hole in the upper top brace (located between the soundhole and neck block). In some cases, this hole is just big enough for a wrench to poke through, but not big enough to accommodate the nut. The brace can be removed, but that is considered a surgical procedure, which is why some luthiers opt to simply enlarge the hole to remove the nut.
Truss rod tools vary, as well.
Some require a hex key (Allen wrench), while others take a flathead or Philips screwdriver, a nut driver, a mini socket wrench, or a small metal rod. To learn more, read “Demystifying Truss-Rod Tools.”
Why truss rod nuts fail.
There are three main reasons why you might have a problem with a truss rod nut:
- Hardware defect.
- The wrong size tool was used in an attempted adjustment.
- The correct tool was used, but it was worn.
A manufacturing defect is pretty rare, but they happen. When you think about how many guitars are built (probably millions each year), there’s a good chance a few lemons are going to squeeze through. It usually comes down to poor quality metal or slight discrepancies in manufacturing tolerances.
Photo 2
Using the wrong tool to adjust a nut is the most common cause of truss rod problems. I’ve seen many nuts that were ruined because someone decided to force the wrong tool around or into them. Photo 2 shows a Fender bullet nut that suffered this fate. Once a socket’s edges have been rounded like this, the hex key can’t grip the nut to turn it.
Photo 3
Recently I removed the neck on a client’s vintage Tele to adjust the truss rod. The nut looked like Photo 3, which illustrates what happens when someone uses a screwdriver that’s the wrong size. The slots get deformed, and this makes truss rod adjustments difficult. The good news is these nuts are easy to remove, even when they’re butchered like this, but unfortunately it’s nearly impossible to find a “period correct” replacement. Sure, there are plenty of aftermarket parts available, but for a vintage guitar, it’s imperative to use period-correct parts to maintain its value. I mention this simply to drive home the importance of using the correct truss rod tool—one that fits snugly.
Worn-out tools will also damage a truss rod nut. For example, if the truss rod requires a hex key and its edges have become worn and rounded, it can in turn round out the inside of the nut. It’s important to check your tools to ensure they won’t damage your guitar.
A basic guitar tech principle: Replacing worn tools is much cheaper than fixing the damage they can cause.
Tools for removing a stripped nut.
There are times when you can use the specified tool to remove the nut, but often you have to be creative. Once when working on a Gibson electric, I had to remove a hex nut that was so stripped that a nut driver wouldn’t grip it. Fortunately, a pair of needle-nose pliers did the job, but you must be careful to avoid stripping the nut more than it already is as you remove it. An improvised tool can easily damage the headstock, so proceed with caution.
Important: Always slacken the strings before you remove the truss rod nut.
Photo 4
In other cases, I’ve used a small flathead screwdriver to extract a nut when a hex key wouldn’t work. For example, by gently tapping the screwdriver into this stripped bullet nut (Photo 4), I was able to get it to catch hold. I turned the screwdriver counter-clockwise and voilà, the nut came off.
I’ve also used a screw extractor, a tool that looks like a drill bit, but with a twist: Screw extractors have tapered, reversed cutting threads designed to dig into a damaged screw and grip it tighter as you turn the extractor counter-clockwise while carefully applying pressure. The counter-clockwise movement backs out the damaged screw—typically its head is mangled or broken off—even as the extractor bores deeper into the screw shaft. I do this manually using a T-handle, but you can also use vice-grips with a screw extractor. I’d advise against using a power drill for extraction, but some techs do, running the drill at slow speeds. Using an extractor to remove a stripped truss rod nut takes a lot of patience, but it’s doable. The trick is to be gentle but firm.
Installing the new truss rod nut.
This is the easy part. Just slide the nut onto the truss rod threads and turn it clockwise. Tighten the nut until it’s just a little snug. Tune the guitar up to pitch and check the relief in the neck. Depending on your playing style, .010" to .012" should be plenty of relief. Check out “Time for a Neck Adjustment?” if you’re not sure how to adjust the truss rod.
Averting disaster.
A stripped truss rod nut is bad news, but it can usually be replaced inexpensively. However, if you strip the threads or nut at the other end of the truss rod—where it screws into hardware embedded within the neck itself—that’s a different story. Also, if the exposed threads on a truss rod are stripped, a replacement nut will not help. In either case, the truss rod itself would need to be replaced—a very invasive and expensive repair. At that point you have to decide whether replacing the neck makes more sense than spending a fortune on major surgery. The bottom line is simple: When adjusting your truss rod, don’t over-tighten the nut.
If you’re not comfortable working with your truss rod nut, consult a qualified repair technician. Guitar techs and luthiers deal with these issues all the time, and paying them for their expertise can be a wise investment.
[Updated 1/25/22]
- Guitar Shop 101: Tips for Buying a Used Electric - Premier Guitar ›
- Guitar Shop 101: “Decking” a Stratocaster Trem - Premier Guitar ›
- DIY: How to Adjust a Truss Rod - Premier Guitar ›
- New Giveaway: Win the Yamaha Pacifica Standard Plus! - Premier Guitar ›
PG’sJohn Bohlinger caught up with Moak at his Nashville studio known affectionately as the Smoakstack.
Grammy-nominated session guitarist, producer, mixer, and engineer Paul Moak stays busy on multiple fronts. Over the years he’s written, played, produced and more for TV sessions (Pretty Little Liars, One Tree Hill) and artists including Third Day, Leeland, and the Blind Boys of Alabama. But most recently he’s worked with Heart and Ann Wilson and Tripsitter.
Time Traveler
Moak is most loyal to a 1963 Stratocaster body that’s mated to a 1980s-vintage, 3-bolt, maple, bullet-truss-rod, 1969-style Fender Japan neck. The bridge has been swapped as many as four times and the bridge and neck pickups are Lindy Fralins.
Cool Cat
If there’s one guitar Moak would grab in a fire, it’s the Jaguar he’s had since age 20 and used in his band DC Talk. When Moak bought the guitar at Music Go Round in Minneapolis, the olympic white finish was almost perfect. He remains impressed with the breadth of tones. He likes the low-output single-coils for use with more expansive reverb effects.
Mystery Message Les Paul
Moak’s 1970 L.P. Custom has a number of 1969 parts. It was traded to Moak by the band Feel. Interestingly, the back is carved with the words “cheat” and “liar,” telling a tale we can only speculate about.
Dad Rocker
Almost equally near and dear to Moak’s heart is this 1968 Vox Folk Twelve that belonged to his father. It has the original magnetic pickup at the neck as well as a piezo installed by Moak.
Flexi Plexis
This rare and precious trio of plexis can be routed in mix-and-match fashion to any of Moak’s extensive selection of cabs—all of which are miked and ready to roll.
Vintage Voices
Moak’s amps skew British, but ’60s Fender tone is here in plentitude courtesy of a blonde-and-oxblood Bassman and 1965 Bandmaster as well as a 2x6L6 Slivertone 1484 Twin Twelve.
Guess What?
The H-Zog, which is the second version of Canadian amp builder Garnet’s Herzog tube-driven overdrive, can work as an overdrive or an amp head, but it’s probably most famous for Randy Bachman’s fuzzy-as-heck “American Woman” tone.
Stomp Staff
While the Eventide H90 that helps anchor Moak’s pedalboard can handle the job of many pedals, he may have more amp heads on hand than stompboxes. But essentials include a JHS Pulp ‘N’ Peel compressor/preamp, a DigiTech Whammy II, DigiTech FreqOut natural feedback generator, a Pete Cornish SS-3 drive, Klon Centaur, and Electro-Harmonix Deluxe Memory Man.
Featuring authentic tape behavior controls and full MIDI implementation, the EC-1 is a premium addition to any guitarist's setup.
Strymon Engineering, the Los Angeles-based company behind premium products for the guitar, plugin, and Eurorack markets, announced a new single-head tape echo pedal in their newer small format today, called the EC-1. Initially based around the award-winning dTape algorithm that helped to make the El Capistan pedal an industry titan, development took a different turn when Strymon acquired an immaculate and heavily modified tube Echoplex® EP-2. The new true stereo pedal features two models of the EP-2’s tube preamp with variable gain, as well as a three-position Record Level switch that allows for additional gain control. Glitchless tap tempo allows tapping in new tempos without tape artifacts, and the Tape Age and Mechanics controls modify a large number of parameters under the hood to deliver authentic tape behavior at any setting. Other features include TRS stereo Ins and Outs, full MIDI implementation, TRS MIDI, arear-panel audio routing switch, USB-C and 300 presets. Being true stereo, the EC-1 processes the left and right inputs independently, allowing it to be placed anywhere in the signal chain.
“We decided to start the project by investigating the preamps from tube echo units, so I bought an original Echoplex® EP-2 to begin the process”, said Gregg Stock, Strymon CEO and analog circuit guru. “It showed up in pristine condition and sounded amazing, and we found out later that it had been heavily modified by storied guitar tech Cesar Diaz. His mods created a single unit with the best attributes of both tube and solid-state Echoplexes, so we spent a bunch of time figuring out how to recreate its behavior.” Pete Celi, Strymon co-founder, and DSP maven said “It was so clean and mechanically stable that other nuances stood out more prominently -chief among them being some capstan-induced variations that help to widen the spectrum of the repeats. With the Mechanics control at around 1 pm, you get a hyper-authentic representation of that golden EP-2 unit, with a high-speed flutter that adds dimension to the echoes.”
EC-1 is available now directly from Strymon and from dealers worldwide for $279 US.
For more information, please visit strymon.net.
Brickhouse Toneworks BH-90 pickups offer the legendary tone of a classic P-90 in a humbucker-sized package, with zero hum.
Brickhouse Toneworks, a new manufacturer of high-quality and innovative guitar pickups, has announced the release of the BH-90 pickup. This hum-canceling design offers the legendary tone and responsiveness of a classic P-90 in a humbucker-sized package -- with absolutely zero hum.
The BH-90 captures the true personality of the beloved single coil P-90 tone – its grit, sparkle, and touch sensitivity to playing dynamics – while eliminating the notorious hum that often limits their use.
Available individually or as matched sets, these pickups effortlessly respond to your playing touch, delivering delicate cleans to aggressive distortion. You’ll get P-90 soul in a humbucker size: the BH-90 seamlessly replaces existing humbuckers with no modifications required. They drop right in where your existing humbuckers live.
Key Features of the BH-90
- Cast Alnico 5 Magnets; 500k Pots & .022uf Cap recommended.
- Ultra quiet: Hum-canceling design, and lightly potted to minimize squeal.
- Classic design: vintage external braided lead wire, with output comparable to vintage '50s P-90
- Bridge: 19.5k (Average), Neck 17.5k (Average). Note: the BH-90’s DCR reading is much higher than normal single coil P-90s due to the nature of their hum-canceling design. This is a case where DCR should not be considered as a measurement of output because these are equivalent in output to a vintage P-90 that ranged in DCR readings between 7-9k.
- Made in the USA with premium quality materials.
The BH-90 street price starts at $170 each and starts at $340 per set.
For more information, please visit brickhousetone.com.
The BH90 by Brickhouse Toneworks | Pickup Demo - YouTube
The final installment with Santa Cruz Guitar Company founder Richard Hoover details the remaining steps that takes a collection of wood and wire into an impeccable instrument. Hoover explains how the company's craftsman delicately sand and finish the acoustics with a light touch to keeps them shiny and singing. He describes the pragmatic reasoning behind finishing the body and neck separately before marrying the two. He describes the balance between mechanical precision with the Plek machine and luthier artistry for the individualistic, hands-on set ups and intonation. Finally, Richard outlines why the company is now designing strings specific to their guitars.