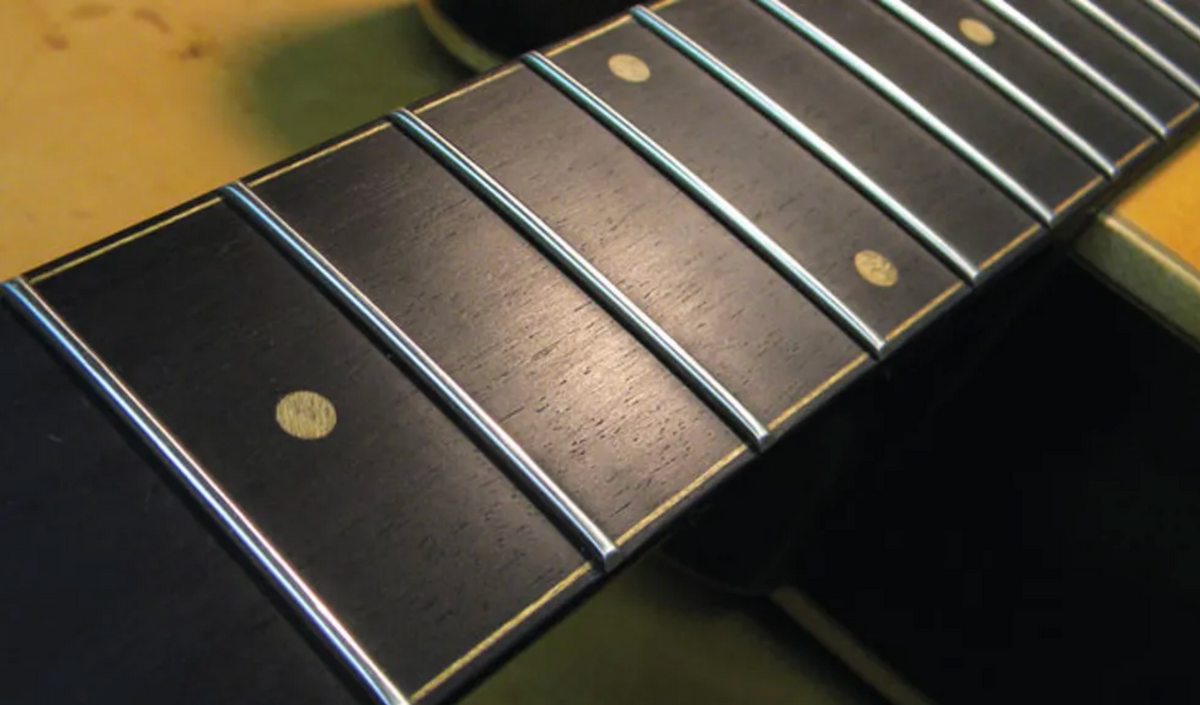
Fig. 1. A clean, well-condition fretboard just begs to be played.
Learn how to clean and condition your guitar and discover why it’s crucial to stay on top of such routine maintenance.
The proper cleaning and conditioning of your instrument is critical to its health. Over the years, I've seen many extreme cases of guitars that were permanently damaged from neglect. Without proper care, a guitar will lose value and eventually become unplayable. However, it's not difficult to clean and condition a guitar—it simply takes a little time and effort. And that's a worthy investment: Keeping your instrument in top condition will save you a lot of money in future repairs.
Fig. 2. Not only does fretboard gunk look unattractive, over time it can damage your instrument.
As we play, dead skin cells, sweat, and dirt build up on the fretboard and collect around the frets. Not only is this unattractive (Fig. 2), but the moisture, acids, and salts in sweat cause the wood around the frets to deteriorate. This can cause dry rot in the fretboard, which results in loose frets and very expensive repairs.
Fig. 3. These frets have become corroded through neglect.
I can always tell if a fretboard hasn't been conditioned when I examine the frets. This is especially noticeable when I'm doing a refret. After I remove the old frets, I can see nasty gunk on the tangs and green corrosion all over the fret wire (Fig. 3).
Fig. 4. If you don't clean and condition your fretboard, it may crack.
Cracks are another terrifying byproduct of not conditioning your fretboard (Fig. 4). When sweat evaporates, it can dry out the fretboard and cause it to crack.
Fig. 5. If they're not cleaned regularly, pickups, potentiometers, and switches can become corroded by the salts and acids in sweat.
A guitar's electronics can also suffer from dead skin cells and sweat. When acids and salts build up on a pickup, they can corrode the coils and magnets and cause the pickup to fail. These corrosive materials have the same effect on potentiometers and switches (Fig. 5).
Many string and accessory manufacturers offer conditioners for your guitar. But be aware that most of these products, including lemon oil, contain harmful chemicals and solvents that will damage your guitar's wood and finish. Avoid anything that contains d-Limonene, alcohol, or silicone.
Derived from oil extracted from citrus rind, d-Limonene contains natural acids. These acids can act as a solvent and break down finishes and cause the wood around the frets to deteriorate. Alcohol dries out the fretboard, bridge, and other unfinished wood, and can cause cloudiness in certain types of finish. Silicone prevents the wood from breathing and can cause the finish on your guitar to become hazy. It's also very difficult to remove.
Fig. 6. When wood isn't sufficiently humidified, it can dry out and crack. This guitar back has seen better days.
Controlling humidity is another important aspect of guitar care. When a guitar gets too dry, the wood cracks (Fig. 6). Conditioning wood certainly helps prevent it from cracking, but it's also a good idea to use a humidifier. New guitars tend to be more prone to humidity cracks than older instruments. Here's why: Most older or vintage guitars were made from air-dried wood. This wood was dried out over several decades, and during this process any pieces that cracked were culled out. The older harvested wood gets, the more stable it becomes, but it's a lengthy, painstaking way to dry wood. Modern guitars are primarily made from kiln-dried wood. Kiln drying is designed to speed up the aging process, but only time can truly age a piece of wood. Guitars made from kiln-dried wood are more susceptible to changes temperature and humidity. Maintaining a guitar-friendly humidity level helps prevent wood from cracking, and we'll discuss how to do this in a moment.
Cleaning and conditioning the fretboard. We'll start by cleaning the fretboard, and the first step here is to remove the strings. Yes, all of them! People often say, “Won't removing all the strings at the same time damage the neck?" The fact is, it won't. Wood has an excellent memory, so you don't have to worry about removing all the strings to service your fretboard. Luthiers do it all the time.
There are several ways to clean a fretboard, and one approach is to use 0000 steel wool. This works great, especially when you want to make your frets shine, but it makes a big mess. Caution: Do not use steel wool on a maple fretboard that has a glossy finish. Rubbing steel wool on any finish will make it hazy.
If you decide to use steel wool, use only 0000 grade. This is the finest steel wool and will not damage the fretboard or frets. If you're cleaning an electric guitar (or an acoustic with a magnetic soundhole pickup), cover the pickups with painter's tape to prevent the steel fibers from collecting around the pole pieces. These very fine steel fibers can cause a pickup to corrode, and they also cause noise if they contact the strings.
Fig. 7. If you opt to clean your fretboard and polish its frets with 0000 steel wool, remember to vacuum up the fibers that inevitably shed during this procedure.
Apply a fretboard conditioner to the fretboard and gently rub the conditioner into the wood with the steel wool pad, turning it frequently. Move across the fretboard, cleaning the wood between the frets, and then work the pad along the side of each fret. Once the fretboard is clean, run the pad up and down along the top of the frets to polish them.
After cleaning the fretboard with steel wool, use a vacuum to carefully remove the steel fibers that inevitably shed from the pad (Fig. 7). Avoid getting the fibers on the guitar's finish, as they can scratch it.
My preferred method for cleaning the fretboard is to use an old toothbrush and Planet Waves Hydrate, a type of fretboard conditioner. This approach is less messy than using steel wool, but it's important to note that Hydrate is only for dark fretboards—don't use it on maple 'boards.
Fig. 8. An alternative to steel wool: Clean the wood with a toothbrush and fretboard conditioner.
I like using a toothbrush because you can scrub all you want without damaging the wood or the frets. Simply spray Hydrate onto your fretboard and work it into the wood and around the frets with the toothbrush bristles (Fig. 8). Once the gunk is loosened, wipe it off with a paper towel. Also be sure you wipe off any excess conditioner to prevent it from coating the strings.
But the toothbrush technique won't polish the frets. If you're not too keen on using 0000 steel wool to do this (and I don't blame you), Planet Waves makes a product called the Fret Polishing System. Basically, it's super-fine polishing paper that's packaged with a protective stiff paper template that covers the wood while exposing the fretwire. The template fits medium or jumbo frets and you can use the kit on maple or dark fretboards.
Fig. 9. Planet Waves' Fret Polishing System includes super-fine abrasive paper and a guard to protect the wood.
Simply lay the template over the fretwire and polish the frets until they glisten (Fig. 9). The kit works great and there is little mess to clean up. But even with this system, you'll want to vacuum the residue off the neck left by the polishing paper.
Fig. 10. Like the fretboard, an acoustic guitar's bridge needs to be cleaned and conditioned.
Cleaning and conditioning a bridge. It's very simple to clean and condition the bridge on an acoustic guitar. Remove the bridge saddle and then scrub the bridge with a toothbrush and conditioner (Fig. 10). Use cotton swabs to clean inside the saddle slot. When the gunk is cleaned off, wipe down the bridge with a paper towel. That's it!
Fig. 11. Filth can build up on a bridge and its saddles. When hardware gets this dirty and rusty, you'll need to disassemble and clean it with WD-40 or 3-in-One oil.
Cleaning the hardware. Sweat is a big enemy of hardware because its acids and salts corrode the metal plating and attract dirt that clogs up any moving parts. In extreme cases, a guitar's bridge (Fig. 11) and tuning keys (Fig. 12) can begin to rust. Cleaning these important mechanisms keeps them looking good and functioning at their best.
Fig. 12. If left on metal hardware, sweat can eat right into the plating and cause rust.
For cleaning metal hardware, I've had success with 3-in-One oil and WD-40. Remember that these products are only safe on metal, so avoid getting them on the fretboard or finish. I typically remove the hardware to clean it with an old toothbrush and then carefully wipe it off before reinstalling.
Cleaning the finish. When cleaning your guitar's finish, avoid furniture polishes like Pledge, which contains lemon oil, or products that contain d-Limonene, alcohol, solvents, or silicone. All of these will damage the finish over time. Sweat is another finish-eater because it causes lacquer to soften and break down.
Water actually works well to clean a guitar finish. Use a slightly damp micro-fiber cloth to wipe away dust and grime, and rinse the cloth frequently to remove any debris. As for a good polish, I only use pure carnauba wax, which is safe for most finishes.
The Issues
Before we discuss how to clean and condition a guitar, it's important to understand where the potential problems lie and why we need to address them.
Two important components to clean, condition, and humidify are the fretboard and bridge. This is crucial because they are typically made of unfinished or untreated wood. Maple fretboards are an exception because they have some type of finish and therefore just need to be cleaned, but not conditioned. Rosewood and ebony fretboards and bridges must be cleaned and conditioned to prevent sweat and dirt from damaging the wood. A clean fretboard not only looks great (Fig. 1), but it feels great under your fingertips.
Fig. 2. Not only does fretboard gunk look unattractive, over time it can damage your instrument.
As we play, dead skin cells, sweat, and dirt build up on the fretboard and collect around the frets. Not only is this unattractive (Fig. 2), but the moisture, acids, and salts in sweat cause the wood around the frets to deteriorate. This can cause dry rot in the fretboard, which results in loose frets and very expensive repairs.
Fig. 3. These frets have become corroded through neglect.
I can always tell if a fretboard hasn't been conditioned when I examine the frets. This is especially noticeable when I'm doing a refret. After I remove the old frets, I can see nasty gunk on the tangs and green corrosion all over the fret wire (Fig. 3).
Fig. 4. If you don't clean and condition your fretboard, it may crack.
Cracks are another terrifying byproduct of not conditioning your fretboard (Fig. 4). When sweat evaporates, it can dry out the fretboard and cause it to crack.
Fig. 5. If they're not cleaned regularly, pickups, potentiometers, and switches can become corroded by the salts and acids in sweat.
A guitar's electronics can also suffer from dead skin cells and sweat. When acids and salts build up on a pickup, they can corrode the coils and magnets and cause the pickup to fail. These corrosive materials have the same effect on potentiometers and switches (Fig. 5).
Many string and accessory manufacturers offer conditioners for your guitar. But be aware that most of these products, including lemon oil, contain harmful chemicals and solvents that will damage your guitar's wood and finish. Avoid anything that contains d-Limonene, alcohol, or silicone.
Derived from oil extracted from citrus rind, d-Limonene contains natural acids. These acids can act as a solvent and break down finishes and cause the wood around the frets to deteriorate. Alcohol dries out the fretboard, bridge, and other unfinished wood, and can cause cloudiness in certain types of finish. Silicone prevents the wood from breathing and can cause the finish on your guitar to become hazy. It's also very difficult to remove.
Fig. 6. When wood isn't sufficiently humidified, it can dry out and crack. This guitar back has seen better days.
Controlling humidity is another important aspect of guitar care. When a guitar gets too dry, the wood cracks (Fig. 6). Conditioning wood certainly helps prevent it from cracking, but it's also a good idea to use a humidifier. New guitars tend to be more prone to humidity cracks than older instruments. Here's why: Most older or vintage guitars were made from air-dried wood. This wood was dried out over several decades, and during this process any pieces that cracked were culled out. The older harvested wood gets, the more stable it becomes, but it's a lengthy, painstaking way to dry wood. Modern guitars are primarily made from kiln-dried wood. Kiln drying is designed to speed up the aging process, but only time can truly age a piece of wood. Guitars made from kiln-dried wood are more susceptible to changes temperature and humidity. Maintaining a guitar-friendly humidity level helps prevent wood from cracking, and we'll discuss how to do this in a moment.
Cleaning and Conditioning the Fretboard.
We'll start by cleaning the fretboard, and the first step here is to remove the strings. Yes, all of them! People often say, "Won't removing all the strings at the same time damage the neck?" The fact is, it won't. Wood has an excellent memory, so you don't have to worry about removing all the strings to service your fretboard. Luthiers do it all the time.
There are several ways to clean a fretboard, and one approach is to use 0000 steel wool. This works great, especially when you want to make your frets shine, but it makes a big mess. Caution: Do not use steel wool on a maple fretboard that has a glossy finish. Rubbing steel wool on any finish will make it hazy.
If you decide to use steel wool, use only 0000 grade. This is the finest steel wool and will not damage the fretboard or frets. If you're cleaning an electric guitar (or an acoustic with a magnetic soundhole pickup), cover the pickups with painter's tape to prevent the steel fibers from collecting around the pole pieces. These very fine steel fibers can cause a pickup to corrode, and they also cause noise if they contact the strings.
Fig. 7. If you opt to clean your fretboard and polish its frets with 0000 steel wool, remember to vacuum up the fibers that inevitably shed during this procedure.
Apply a fretboard conditioner to the fretboard and gently rub the conditioner into the wood with the steel wool pad, turning it frequently. Move across the fretboard, cleaning the wood between the frets, and then work the pad along the side of each fret. Once the fretboard is clean, run the pad up and down along the top of the frets to polish them.
After cleaning the fretboard with steel wool, use a vacuum to carefully remove the steel fibers that inevitably shed from the pad (Fig. 7). Avoid getting the fibers on the guitar's finish, as they can scratch it.
My preferred method for cleaning the fretboard is to use an old toothbrush and Planet Waves Hydrate, a type of fretboard conditioner. This approach is less messy than using steel wool, but it's important to note that Hydrate is only for dark fretboards—don't use it on maple 'boards.
I like using a toothbrush because you can scrub all you want without damaging the wood or the frets. Simply spray Hydrate onto your fretboard and work it into the wood and around the frets with the toothbrush bristles (Fig. 8). Once the gunk is loosened, wipe it off with a paper towel. Also be sure you wipe off any excess conditioner to prevent it from coating the strings.
But the toothbrush technique won't polish the frets. If you're not too keen on using 0000 steel wool to do this (and I don't blame you), Planet Waves makes a product called the Fret Polishing System. Basically, it's super-fine polishing paper that's packaged with a protective stiff paper template that covers the wood while exposing the fretwire. The template fits medium or jumbo frets and you can use the kit on maple or dark fretboards.
Fig. 9. Planet Waves' Fret Polishing System includes super-fine abrasive paper and a guard to protect the wood.
Simply lay the template over the fretwire and polish the frets until they glisten (Fig. 9). The kit works great and there is little mess to clean up. But even with this system, you'll want to vacuum the residue off the neck left by the polishing paper.
Cleaning and Conditioning a Bridge.
Fig. 10. Like the fretboard, an acoustic guitar's bridge needs to be cleaned and conditioned.
It's very simple to clean and condition the bridge on an acoustic guitar. Remove the bridge saddle and then scrub the bridge with a toothbrush and conditioner (Fig. 10). Use cotton swabs to clean inside the saddle slot. When the gunk is cleaned off, wipe down the bridge with a paper towel. That's it!
Cleaning the Hardware.
Fig. 11. Filth can build up on a bridge and its saddles. When hardware gets this dirty and rusty, you'll need to disassemble and clean it with WD-40 or 3-in-One oil.
Sweat is a big enemy of hardware because its acids and salts corrode the metal plating and attract dirt that clogs up any moving parts. In extreme cases, a guitar's bridge (Fig. 11) and tuning keys (Fig. 12) can begin to rust. Cleaning these important mechanisms keeps them looking good and functioning at their best.
For cleaning metal hardware, I've had success with 3-in-One oil and WD-40. Remember that these products are only safe on metal, so avoid getting them on the fretboard or finish. I typically remove the hardware to clean it with an old toothbrush and then carefully wipe it off before reinstalling.
Cleaning the Finish.
When cleaning your guitar's finish, avoid furniture polishes like Pledge, which contains lemon oil, or products that contain d-Limonene, alcohol, solvents, or silicone. All of these will damage the finish over time. Sweat is another finish-eater because it causes lacquer to soften and break down.
Water actually works well to clean a guitar finish. Use a slightly damp micro-fiber cloth to wipe away dust and grime, and rinse the cloth frequently to remove any debris. As for a good polish, I only use pure carnauba wax, which is safe for most finishes.
Controlling Humidity
Once your guitar is clean, you'll want to protect the wood with some type of humidifier. For a guitar that's stored in its case, I recommend the Humidipak from Planet Waves. It's a simple, accurate, and effective way to maintain the ideal humidity for your guitar. If you keep your guitar out in a studio or living area, try running an ultrasonic or warm mist humidifier in that room. For most stringed instruments, the optimum humidity level is 45 percent.
[Updated 3/24/22]
- Guitar Shop 101: Curing Sticky-Neck Syndrome - Premier Guitar ›
- Mod Garage: Cleaning Up an Acoustic from the Inside - Premier Guitar ›
- Guitar Shop 101: Safe Ways to Clean Your Guitar's Finish - Premier Guitar | The best guitar and bass reviews, videos, and interviews on the web. ›
- Guitar Shop 101: Curing Sticky-Neck Syndrome - Premier Guitar ›
- Mod Garage: Ritchie Blackmore Stratocaster Mods - Premier Guitar ›
- Mod Garage: The Truth About Putting Vintage Parts Into New Guitars - Premier Guitar ›
- Ugly Amps “Lil” Ugly Review - Premier Guitar ›
- Watch a ’59 Strat & a ’59 ES-335 Get Refretted in Under 10 Minutes - Premier Guitar ›
- The Inexpensive, Everyday Tools That Live on My Workbench - Premier Guitar ›
This wonky Zim-Gar was one of many guitars sold by importer Gar-Zim Musical Instruments, operated by Larry Zimmerman and his wife.
The 1960s were strange days indeed for import guitars, like this cleaver-friendly Zim-Gar electric.
Recently I started sharing my work office with a true gem of a guy … one of the nicest fellas I’ve ever come across. If you’ve been following my column here, you might remember my other work mate Dylan, who is always telling me about new, fad-type things (like hot Honey guitars) and trying to convince me to use AI more. (What can I say, he’s a millennial.) But Steve, on the other hand, is about 10 years my senior and is a native New Yorker—Brooklyn actually, from the Canarsie neighborhood. Steve is a retired teacher and spent many years teaching in the Brownsville area of Brooklyn, and man, he has some amazing stories.
Mostly we talk about music and sports (he’s exiled here among us Philadelphia sports fans) and he’s just endlessly interesting to me. He has a huge appetite and can eat a whole pizza. When he talks, he sounds like one of the Ramones and he still has an apartment in Rockaway Beach. We both love Seinfeld and, like George Costanza, Steve knows where all the great bathrooms are across New York City. Since he’s been added to my circle (and is such a mensch), I decided I should work him into a column.
So here’s the connection: Back in the day there were many American importers, dealers, and wholesalers. A lot of them were based in New York, Chicago, and Los Angeles, but I only know of one guitar importer located in Brooklyn: Gar-Zim Musical Instruments. The company was run by Larry Zimmerman and his wife, and the couple had some success importing and selling Japanese guitars and drums. I used to see early Teisco imports with the Zim-Gar badge, which was the brand name of Gar-Zim. I’ve also seen Kawai guitars with the Zim-Gar label, but the Zimmerman’s seemed to sell cheaper and cheaper gear as the ’60s wore on, including the piece you see here.
“This build reminds me of the cutting boards I used to make in wood shop back in my high school days.”
The model name and factory origin of this guitar is a mystery to me, but this build reminds me of the cutting boards I used to make in wood shop back in my high school days. The guitar is just flat across the top and back, with absolutely no contouring or shaping. Its offset body is plywood with a thin veneer on the top and back. From a distance this guitar actually looks kind of nice, but up close you can see a rather crude and clunky instrument that offers little flexibility and playability. The non-adjustable bridge is off center, as is the tremolo. It was really hard to get this guitar playing well, but in the end it was worth it, because the pickups were the saving grace. Another example of gold-foils, these units sound strong and raw. The electronics consist of an on/off switch for each pickup and a volume and tone knob. The tuners are okay, and the headstock design is reminiscent of the Kay “dragon snout” shape of the mid to late ’60s, which is where I would place the birthdate of this one, probably circa 1966. Everything is just so goofy about this build—even the upper strap button is located on the back of the neck. It reminds me of that era when simple wood factories that were making furniture were tasked with building electric guitars, and they simply didn’t know what they were doing. So, you get oddities like this one.
Gar-Zim continued to sell guitars and other musical instruments through the 1970s and possibly into the ’80s. I once even saw a guitar with the label Lim-Gar, which is totally puzzling. I think there should’ve been a Stee-Gar designation for my new buddy Steve-o! Yes, good readers, with guitars and me, there are always just a few degrees of separation.
In line with the MOOER’s recent expansion on the MSC range, the company is excited to announce the new MSC50 Pro, an Alder-bodied electric guitar with gloss finish, available in the new Magic Crystal color.
Featuring a roasted maple neck with a satin finish, a rosewood fingerboard for playing comfort, 22 frets, and a standard C shape, the guitar has been designed with classic guitarists in mind. This is beautifully emphasized with its beautifully resonant tonewoods, all while still being balanced perfectly with style and comfort of use.
The MSC50 Pro features all of the industry-standard features you might expect from such an impressively affordable guitar, such as bolt-on construction, a bone nut, and a dual-action steel truss rod. However, other features make the electric guitar stand out among others at a similar price point, such as its MTN-3LC locking tuning pegs, beautiful Abalone dot inlay, and, of course, its previously mentioned tonewood selection.
In order to capture the MSC50 Pro's balanced tonal profile, MOOER's luthiers have built it with three perfectly balanced pickups: the MSC-II N single coil neck pickup, the similar MSC-II M single coil middle pickup, and, best of all, the MHB-II B bridge humbucker. When these carefully chosen pickups are combined with the guitar's MPW 2-point chrome bridge, guitarists can make the most out of its tonal versatility, all while maximizing tuning stability.
To ensure that the guitar is suitable for a wide range of genres, both softer and higher-gain examples, the MSC50 Pro has a convenient coil split switch built into it, giving users better resonance control. Of course, this is also combined with a classic tone dial, a standard 5-way tone switch, and a volume control dial.
Overall, the MSC50 Pro reminds users of MOOER guitars that the company has never forgotten about its roots in classic-style guitars. Yes, the company is continuing to develop innovative guitar technology in other areas, but this electric guitar also represents a grounded approach, keeping things classic, sleek, and tonally versatile–all at a reasonable price point.
Features:
- Alder Body with a Gloss Finish
- Available in the Magic Crystal color
- Standard C-shaped roasted maple neck with a Satin finish
- Bolt-on construction
- 22-fret rosewood fingerboard
- Abalon dot inlay
- MTN-3LC locking tuners
- Bone nut
- Dual-Action Steel Truss Rod
- 12" radius
- 09-46 strings
- 25.2" scale
- MSC-II N Single Coil neck pickup, an MSC-II M Single Poil middle pickup, and an MHB-II B Humbucker Bridge Pickup
- Chrome guitar strap pin
- Coil Split Switch
- 5-Way Tone Switch
- Volume and tone dials
- MPW 2-Point chrome bridge
The MSC50 Pro will be available from the official distributors and retailers worldwide on 13th May 2025 at an expected retail price of USD419/Euro399/GBP339.
MOOER Expands Its Popular MSC Guitar Line with the MSC30 Pro and MSC31 Pro
MOOER has never shied away from innovation when it comes to its guitars. However, with the recently announced release of the MSC30 Pro and MSC31, the company reminds us that, sometimes, true innovation lies in mastering and enhancing a proven classic. With this philosophy, MOOER introduces two new exciting additions to their beloved MSC series of electric guitars.
Both the MSC30 Pro and MSC31 Pro continue MOOER’s philosophy of creating affordable guitars, but without sacrificing quality or performance, thanks to the poplar bodies and flame maple tops. Some guitarists will be drawn to the bright tones of the MSC30 Pro’s maple fingerboard, whereas others will prefer the warmer resonance of the MSC31 Pro’s rosewood alternative.
Each guitar features sturdy bolt-on neck construction, dual-action steel truss rods, bone nuts, and MTN-1 chrome tuning pegs (with the BK upgrade being reserved for the MSC31 Pro), ensuring tuning stability and comfort at all times.At the heart of both models are MOOER’s versatile MSC pickups, comprising the MSC-1N single-coil neck pickup, the MSC-1M single-coil middle pickup, and the powerful MHB-1B dual-coil humbucker at the bridge. Further complemented by a versatile 5-way pickup selector and exclusive coil split switch, players can effortlessly switch between a wide palette of tones, such as pristine cleans ideal for jazz or blues, or high-gain tones for heavier genres.
Tremolo support is also provided through both the guitar's bridges, with the MSC30 Pro featuring an MTB-1 2 Point Tremolo bridge, and the MSC31 Pro boasting an exclusive black MTB-1 BK 2 Point Tremolo bridge. Both bridges guarantee guitarists the ability to use tremolo bars in their guitar performances, without compromising the integrity of tuning stability.
Both guitars come with a selection of vivid new colors, complementing the guitar’s hardware with undeniable visual appeal. The MSC30 Pro is available in the classic finishes of Sunset Red, Lake Blue, Lemon Green, and Rose Purple. Meanwhile, the MSC31 Pro boasts its own selection of glossy finishes: Grey Burst, Blue Burst, Green Burst, and Purple Burst.
Overall, the MSC30 Pro and MSC31 Pro solidify MOOER’s commitment to combining quality craftsmanship, affordability, and versatility, giving guitarists of all levels the chance to own instruments that genuinely inspire.
Features
MSC30 Pro:
- Classic S-style design
- Poplar body with flame maple top
- Maple fingerboard
- Maple neck with satin finish
- Bolt-on neck construction
- 22 nickel silver frets, Abalone dotted inlay
- Coil split switch and versatile 5-way pickup selector
- MSC-1N/M single-coil pickups and MHB-1B humbucker
- 25.5" scale
- MTN-1 Chrome tuning pegs
- Available in gloss-finished Sunset Red, Lake Blue, Lemon Green, and Rose Purple
- Volume and tone dial
- Chrome strap pin
MSC31 Pro:
- Classic S-style design
- Poplar body with flame maple top
- Rosewood fingerboard
- Maple neck with satin finish
- Bolt-on neck construction
- 22 nickel silver frets, White Shell dotted inlay
- Coil split switch and versatile 5-way pickup selector
- MSC-1N/M single-coil pickups and MHB-1B humbucker
- 25.5" scale
- MTN-1 BK tuning pegs
- Available in gloss-finished Grey Burst, Blue Burst, Green Burst, and Purple Burst
- Volume and tone dial
- Chrome strap pin
The MSC30 Pro and MSC31 Pro will both be available from the official distributors and retailers worldwide on 2nd April 2025.
MOOER Gives Bassists What They Want with the New MBJ410 and MBJ420 Electric Bass Guitar Models
For 15 years, MOOER has built a critically acclaimed name for itself thanks to its cutting-edge electric guitars, pedals, and accessories. While the company is no stranger to building electric bass guitars, this has not been its focus for some time, hence why so many bassists are excitedly anticipating the release of the MBJ410 and MBJ420 electric bass guitars.
Both the bass guitars sport glossy Poplar bodies, keeping the price point affordable but without limiting their tonal resonance and versatility, whereas the MBJ420 holds the additional bonus of being built with a Poplar Burl top. Complete with roasted maple C-shaped necks (also accented with a gloss finish) as well as Roasted Maple fingerboards and White Shell dot inlays, the necks are designed to offer as much comfort as possible–a high priority for bass guitarists.
A 34" fret scale further enhances practicality for bassists, as does the neck's 12" radius. Strings are available in .045, .065, .080, and .100 gauges, providing something for any type of bass style - whether slapping, plucking, or picking techniques are preferred.Thanks to the industry-standard components of a dual-action steel truss rod and bone nut, the tuning and resonant stability of both the MBJ410 and MBJ420 models are also of a high standard. However, this is accentuated further by the guitars' strong and reliable BTN-1 tuning pegs, essential for heavier-gauge bass strings.
The tonewoods and structural integrity of the MBJ-series electric bass guitars wouldn't be complete without the accompaniment of the guitar’s two single-coil JB-style pickups. Combined with the MOOER BSC-2 bridge, both bass guitars have been carefully designed to amplify bass resonances excellently, complemented even further by their simple but effective tone dials. Two volume controls are also built in, ensuring that bassists can customize their sonic output to have the perfect tonal blend.
In terms of standout features, the main difference between the two bass guitars is the MBJ420's added poplar burl top, but most notably, the color selections. For the MBJ410, the bass guitar is available in Gunmetal Gray, Metal Green, and Metal Blue, perfectly suiting the stages of higher-gain performances. In contrast, the aesthetics of the MBJ420 are more classic, purchasable in Red Burst, Blue Burst, and Tobacco Burst. Finally, both guitars are topped with a chrome strap pin, enabling stylish and energetic live performances.
Overall, bassists will no doubt be excited to see MOOER return to electric bass guitars with the MBJ410 and 420 models. Of course, electric guitars will remain the focus for the company, but the release of these two new products is a reminder of just how accommodating MOOER is for its wide audience of musicians.
Features
- Electric bass guitar built with gloss-finished Poplar body (MBJ420 also features a Poplar Burl Top)
- Roasted maple C-shaped neck with a gloss finish
- Roasted maple fingerboard
- White Shell dot inlay
- 12” neck radius
- MOOER BSC-2 bridge
- VBJ-1 and VBJ-2 Single Coil pickups
- MOOER BTN-1 tuning pegs
- Bolt-on construction
- Bone nut
- Dual-action steel truss rod
- Pre-installed strings available in .045, .065, .080, and .100 gauges
- 21 frets
- 34"fret scale
- Colors available in Gunmetal Gray, Metal Green, and Metal Blue (MBJ410), and Red Burst, Blue Burst, and Tobacco Burst (MBJ420)
- Chrome strap pin
- 2 x volume control dials
- 1 x Tone dial
The MBJ410 and MBJ420 will both be available from the official distributors and retailers worldwide on 29th April 2025 at an expected retail price of USD319/Euro299/GBP249(MBJ410), USD399/Euro379/GBP319(MBJ420).
The Oceans Abyss expands on Electro-Harmonix’s highly acclaimed reverb technology to deliver a truly immersive effects workstation. The pedal is centered around dual reverb engines that are independently programmable with full-stereo algorithms including Hall, Spring, Shimmer and more. Place these reverbs into a customizable signal path with additional FX blocks like Delay, Chorus, Tremolo, or Bit Crusher for a completely unique soundscape building experience.
Electro-Harmonix has paved the way for powerful, accessible reverbs since the release of the original Holy Grail and now we’ve pushed the envelope deeper with the fully-equipped Oceans Abyss. Featuring a customizable signal path with up to 8 effects blocks, the Oceans Abyss can be configured as individual reverb, modulation, EQ, delay, bit crusher, saturation or volume effects, or as countless combinations for incredibly creative effect shaping. From a simple Spring reverb to a lush stereo field featuring stereo hall and shimmer reverbs, chorus, delay, overdrive, and tremolo, you can go from surf to shoegaze instantly, without breaking a sweat.
Deep parameter editing is accessible via the high-visibility OLED display with multiple graphical views and easy-to-read designs. Expression/CV control over nearly every parameter gives artful control of your effects and dynamics. Fully-stereo I/O plus an FX Loop allows for use with any instrument, recording set up, or live rig. 128 programmable presets via onboard footswitching or MIDI ensure perfect recall in all performance situations. MIDI IN/OUT ports with MIDI IN support of PC, CC, and Tempo Clock expand the already immense talents of the Oceans Abyss. Connect with UBS-C to Windows or Mac for effects editing, preset management, and more with the free EHXport™ app (coming soon).
- Two Stereo Reverbs available at once, each fully pannable in the stereo field
- 10 reverb types to choose from: Room, Hall, Spring, Plate, Reverse, Dynamic, Auto-Infinite, Shimmer, Polyphonic, Resonant
- Additional FX blocks: Delay (Digital, Analog and Tape emulations), Tremolo, Chorus, Flanger, Phaser, Graphic EQ, Saturation, Bit Crusher, External FX Loop, Volume
- Create custom signal path routing with up to 8 effects blocks. Two blocks may be re-verb, the rest may be any of the additional FX blocks.
- Infinite reverb sustain with the press of a footswitch
- Stereo Audio I/O
- Stereo FX Loop routing on TRS Jacks
- Dual action footswitches allow for momentary or latching use
- Easily enable or disable tails
- 128 fully customizable presets
- All controls can be saved to presets
- Dive deep into global and preset settings to set up Oceans Abyss for your specific needs
- Illuminated slide pots and buttons
- High-visibility OLED graphical display
- Multiple graphical views: Signal Path, Performance, Settings, Physical, Explorer
- Easy-to-navigate menu system
- Ergonomic NavCoder knob allows rotary and directional navigation through menus
- EXPRESSION / CV input to control nearly any parameter in any FX block
- Footswitch input allows for adding up to three external footswitches, each assigna-ble to a number of functions
- MIDI In and Out. MIDI IN supports PC, CC (over nearly every available parameter), and Tempo Clock
- USB-C port to connect to Windows or Mac and interface with EHXport™ app (coming soon)
- 96kHz / 24-bit sample rate conversion
- Supplied with 9.6VDC / 500mA power supply
Our columnist’s silver-panel Fender Bandmaster.
How this longstanding, classic tube amp design evolved from its introduction in 1953.
I have a silver-panel Bandmaster Reverb that I don’t think I’ve talked about enough in this column. It’s one of the most versatile and flexible amps I own, so I use it for everything. It’s portable, has tube-driven reverb and tremolo, and has a full set of EQ knobs including the critical bright switch, which we discussed the importance of earlier this year (“How to ‘Trebleshoot’ a Vintage Fender Amp,” March 2025). The amp is not only pedal-friendly; the flexible 4-ohm output impedance will handle almost all speaker configurations and sound any way you’d like. Let’s take a deeper look at the Fender Bandmaster amp and walk through its development through the years.
The first Bandmaster was introduced in 1953 as a wide-panel tweed amp with Fender’s 5C7 circuit. This rare combo was loaded with a single 15" Jensen P15N and powered by dual 6L6GC tubes in push-pull configuration to produce a modest 25 watts. The 6L6GCs were cathode biased and along with the 5U4GB rectifier tube contributed to a forgiving sag, early breakup, and a midrange-y voice.
Fender made several changes when they launched that amp’s successor in 1955, the more widely known 5E7 narrow-panel Bandmaster, a well-proven amp that has come back as a reissue model. It was still a dual-channel amp—instrument and microphone—but the newer 5E7 model had a fixed bias and a negative feedback loop, providing a louder, firmer, and cleaner tone. Most importantly, the single 15" speaker was replaced by three 10" speakers, making it very similar to the narrow-panel tweed Bassman, the granddaddy of all Marshall amps. This Bandmaster had three speakers instead of the Bassman’s four, and it delivered 25–30 watts instead of 40. It offered early breakup with a midrange-y, big and full tone.
For those not acquainted with tweed amps, the volume and EQ knobs behave differently than on silver- and black-panel Fender amps. The volume pot can act like a distortion control, while the EQ knobs control the volume, and many players I’ve talked to have not really unlocked this secret. This works because, in these circuits, the volume pot sits right before the preamp tube, which allows it to push the tube into full distortion. Since the EQ pots are located right after and are capable of reducing the volume, you’re able to distort the preamp at low volume settings.
“Things became more standardized in 1964 with the arrival of the black-panel AB763 Bandmaster, an amp I have worked on a lot and appreciate for its robustness, simplicity, and versatility.”
In 1960, a short-lived and rare Bandmaster dressed in brown tolex and a black faceplate appeared with the 5G7 circuit. From here on, all Bandmasters had the modern top-mounted chassis. With this circuit, the Bandmaster started to both look and sound more like a black-panel amp. It kept the 3x10" speakers but got a diode rectifier and bigger transformers resulting in a 45-watt output. Tremolo was introduced for the first time, and both channels were now intended for guitar.
The following year, a blonde 6G7 Bandmaster followed as a smaller amp head paired with a 1x12 extension cabinet. It had the timeless early blonde looks with cream tolex, brown faceplate, oxblood grill cloth, large Fender logo, and white knobs. But halfway into the blonde era, towards 1964, things turned strange and rather confusing. There were suddenly two 12" speakers, black knobs, a wheat-colored grill cloth, a more slim black-panel-style Fender logo, a black faceplate, and all in various combinations close to the transition into ’64.
Things became more standardized in 1964 with the arrival of the black-panel AB763 Bandmaster, an amp I have worked on a lot and appreciate for its robustness, simplicity, and versatility. It offers a pure, clean, scooped black-panel tone that’s somewhere between a Vibrolux Reverb and Pro Reverb, which share the medium-sized 125A6A output transformer and dual 6L6GC tubes. With its medium/high power and flexible 4-ohm output impedance, it can drive all kinds of speaker cabinets—as long as you stay between 2 and 8 ohms, you are safe.
For a short time in 1967–68, there was a transitional Bandmaster with aluminum trim and black-panel innards before the all-new silver-panel Bandmaster Reverb replaced it in 1968. The small-head cabinet had grown in size and, unfortunately, weight to accommodate the reverb tank. The amp got a 5U4GB rectifier tube along with a few general silver-panel changes to the circuit. Several silver-panel models existed with minor differences until a 70-watt beast version came along in 1977 with master volume.
To my own 1968 Bandmaster Reverb, I have done a few adjustments. First, I made a custom baffle to hold two 8" speakers. I installed a pair of WGS G8C speakers that fit perfectly on the baffle board without colliding with the reverb tank or transformers. Sometimes, I use only one of the 8" speakers for bedroom volume levels. Second, I reversed the bias circuitry to standard AB763 specs, making it easier to adjust bias correctly on both power tubes. If you are into sparkling clean and funky Strat sounds, you would love this little 2x8" combo.